Since the first cargo-only flight, which took place about a century ago, the airfreight industry has evolved significantly. It passed from being airmail centered to gradually expanding into other types of commodities. Advancements in aircraft technology made this transporting solution faster than any other method. Over time, its popularity became undeniable. But it was not until the rise of the internet in the ’90s that air shipping experimented a major growth.
This development can be traced back to a combination of factors. On the one hand, the global network gave validity to air transportation by making it more accessible and reliable. The digitalization opened new possibilities for managing and tracking shipments regardless of location and time. With the boom of e-commerce and express parcel delivery more companies relied on air cargo to export products anywhere.
Today, airfreight operations are transforming to capitalize on online trade while dealing with the challenges set by the coronavirus outbreak. Building global standards and fostering innovative thinking are the basis to ensure the flow of goods beyond the borders. Whether continuing operating or not will depend on the capacity of carriers to adhere to current governmental guidelines and to generate synergies with other stakeholders.
These aspects are crucial for keeping airfreight operations running
1. Conducting basic sanitary procedures when handling cargo
There is still no conclusive evidence suggesting a transmission of coronavirus through direct contact with packages. However, research shows that this virus may survive for up to 72 hours on surfaces such as plastic and stainless steel. For this reason, the World Health Organization (WHO) encourages to follow basic disinfection procedures to prevent possible contagious.
Personal protective equipment (PPE), like masks and gloves, could be effective for reducing COVID-19 spread. Due to the current shortage of PPE, the WHO calls for a rationalized use of it in sectors other than healthcare. So, it is advised, before distributing protective gear, to instruct personnel on how to wear it correctly.
Special considerations apply to the manipulation of consignments coming from most affected countries. Good practices include:
- Enhanced aircraft cleaning after unloading. The method of spray disinfection using a 60%-alcohol agent is particularly suitable for its wide coverage.
- Routine sterilization of frequently touched surfaces especially in ground vehicles.
- To check before application what is the minimum contact time for the sanitizing solution to react.
- Wiping scanners, two-way radios, and other shared devices at least once per shift.
- Discarding “re-usable” gloves periodically, even if slightly damaged.
- And most important − face-touching is No-Go! Putting on gloves does not replace appropriate hand hygiene.
Good to know >> Are some of the packages to be handled visibly dirty from body fluids? The Centers for Disease Control and Prevention (CDC) urges ramp agents to carefully separate all contaminated objects and to communicate this immediately to the supervisor.
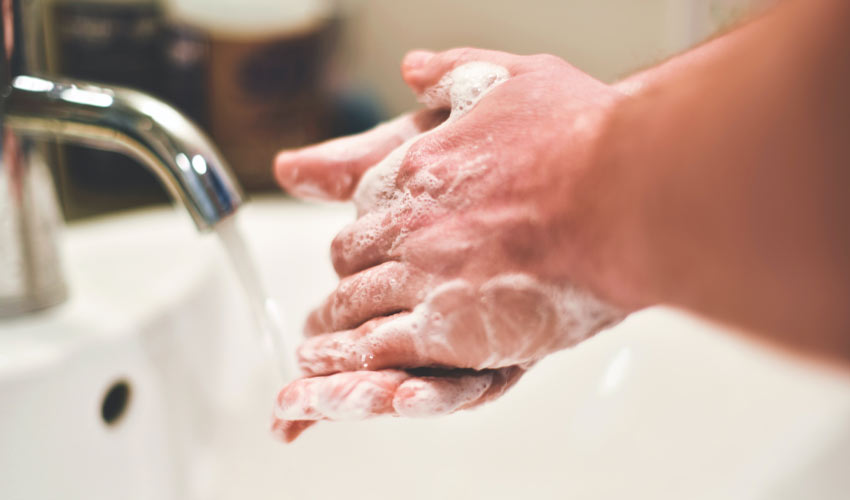
2. Paying attention to physical distancing rules when planning staff
Health authorities recognize that minimizing contact with other individuals reduces further escalation of this sanitarian crisis. In consequence, physical distancing guidance should be followed as far as reasonably possible. According to the WHO, it is ideal to maintain at least 1 m between fellow workers. But what if the nature of the performing tasks makes it difficult to do so?
Since the demand for air cargo continues growing, it is reasonable to think, that additional manpower will be needed. That is the case of short-haul flights where rapid turnarounds depend upon several ramp agents working at a time. To hinder overlapping schedules, an optimal workload calculation becomes crucial. Moreover, planning based on what-if scenarios is a smart way to cover shifts, when operational irregularities pop up.
3. Improving Unit Load Device Management (ULD)
In this challenging era, speed and efficiency constitute valued commodities. The urgency for basic supplies has marked a before and after in the air transportation sector. To avoid bottlenecks, it is paramount that the necessary equipment stays ready for service. Making sure the right Unit Load Device is available in the right place, moment, and conditions is key for saving costs.
Some handling recommendations include to:
- Remind personnel to not store ULDs directly on the ground but on a suitable base support system.
- Remove all rubbish and auxiliary accessories after finishing parcel loading.
- Park pallets horizontally while containers shall be positioned base downwards.
- Tag damaged units to facilitate their identification and segregation from the operative ones. Here can operators refer to the Airport Handling Manual (AHM) 420.
- Reduce the exposure to direct sunlight, water, and extreme temperatures.
- Ensure adequate training for staff in charge of their manipulation.
4. Reaching agreements with airport operators regarding slot allocation
If arriving and departing times were not coordinated, major airports would run into chaos. Even with the downturn of passenger traffic, slot allocation is a work that should not be overlooked. Perhaps due to the impact of coronavirus on commercial air travel, it is easier for freight service providers to secure airport slots. However, the requirements that airlines must satisfy to maintain such permissions are far from being adjusted to the current context.
Rules governing slot administration outline that carriers must operate 80% of their allocated slots under normal circumstances. If not, they might lose their utilization rights for the upcoming season. Although the volume of goods transported by air tends to increase, it is still below the levels showed in the previous year. The International Air Transport Association (IATA) calls for reaching agreements to temporally relax these regulations to face today´s emergency. With the cooperation of authorities, airfreight operations can be optimized towards a more sustainable capacity utilization.
In Conclusion: A proactive approach can safeguard the functionality of air cargo
There are plenty of lessons to learn from what the world is currently experiencing. The COVID-19 has exposed the urgency to improve things. Taking a passive attitude can only threaten the recovery of the global supply chain and the economy. For getting back to normal is airfreight a major player. But is this sector prepared to rethink its crisis management procedures and so, prevent operative disruptions? Incorporating sanitary measures, training employees, providing them with the necessary protective equipment, managing schedules as well as setting up discussion channels with partners serve as a basis for developing suiting emergency plans. The time has come to embrace change towards building resilience for the future.
0 comments on “Recommendations for Airfreight Operations during COVID-19”